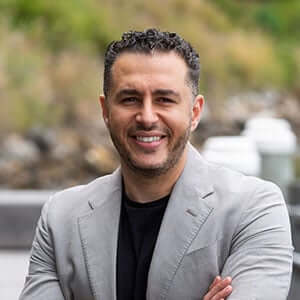
To effectively mitigate risk in the supply chain, it is crucial for organisations to develop agile and resilient systems that can handle the growing frequency and magnitude of disruptions. The supply chain industry has experienced a significant increase in disruptive events over the past decade, emphasising the need for businesses to proactively manage crises and build resilience for the future.
Supply chain management is an integral part of any business, playing a vital role in ensuring that products or services are delivered to customers on time and at a reasonable cost. However, managing a supply chain can be challenging, particularly when it comes to mitigating risks.
In this blog post, we will explore efficient strategies that businesses can use to mitigate risk in supply chain management.
How to mitigate risk in your supply chain
Supply chain management is a complex process, and there are many factors that can disrupt it, such as oil crises, wars, pandemics and security hacks. Unfortunately, it’s impossible to predict when such events will occur.
However, instead of worrying about the unpredictable, supply chain managers should focus on what they can control. These are 9 efficient strategies that organisations can implement to reduce risk and build a more resilient supply chain.
1. Build redundancy into your ERP system
In today’s digital age, cyberattacks have become increasingly common, with ERP systems being a prime target. If your ERP system, which is the lifeblood of your business, is compromised, it can have a catastrophic impact on your business.
Therefore, supply chain leaders need to work closely with IT security and risk management leaders to develop joint cybersecurity risk management approaches to their business.
One way to mitigate this risk is by having alternate solutions that do not rely entirely on ERP systems for critical data transfer. For instance, a separate system that provides information about the location of your assets independent of your ERP system can help control, mitigate, and compartmentalise risks.
Boards are increasingly discussing ways to mitigate the impact of cyberattacks on supply chains, particularly Distributed Denial of Service (DDoS) attacks on ERP systems. One way to address this concern is by relying on third-party asset location solutions running on the 0G network, which is highly secure by design and less susceptible to network attacks. This makes it ideal for Industrial Internet of Things (IIoT) applications.
By leveraging 0G network technology, businesses can ensure that they have a backup option in case their ERP system is compromised. They will have valuable information about where all their shipments and containers are located across their supply chain.
This approach can help build in redundancy to reduce the risk of supply chain disruption due to cyberattacks.
2. Improve asset visibility now
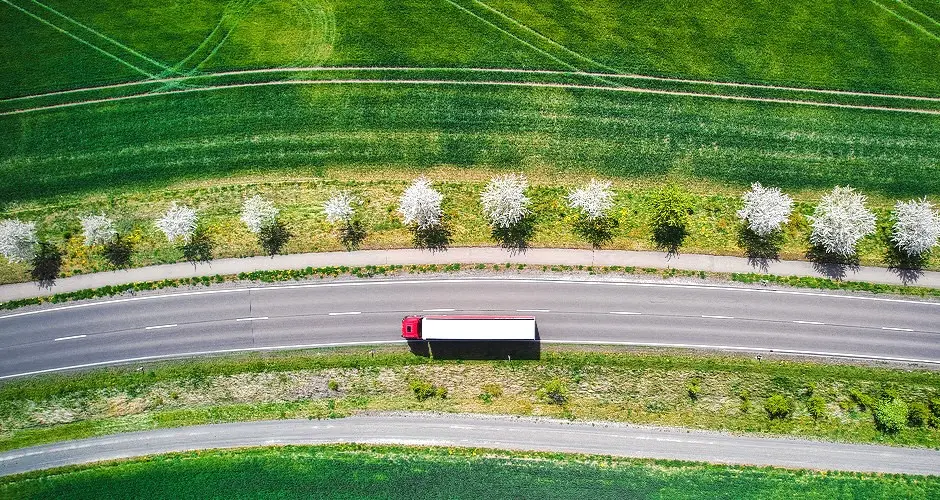
A quick way to mitigate risks in your supply chain is to know where your assets are located, and their condition.
Investing in secure and effective tracking technologies is imperative because it helps identify risks and addresses them proactively. This means faster reaction times when things go wrong, allowing you to rapidly identify and address disruptive demand and supply situations and secure alternate suppliers. You can’t manage what you can’t measure, so ultimately, visibility builds resilience in your supply chain.
This is where Industrial Internet of Things (IIoT) can assist. More and more global supply chain businesses are realising the benefits of IIoT, especially through 0G technology.
0G technology is designed to serve use cases where communication range must reach further, penetrate dense physical structures and allow battery-operated infrequent communication devices to last in the field for extended periods of time.
The 0G Network is ideal for supply chain asset tracking, smart utilities, smart building, and smart park applications, among others. The IoT is already revolutionising many of these industries.
A prime example of this is CouriersPlease, a leading parcel delivery service that implemented a flexible IoT-enabled asset tracking solution. This innovation has enabled CouriersPlease to gain real-time visibility into the location of each individual parcel cage, significantly reducing losses and optimising distribution amid their rapid business growth. By tracking 3,500 parcel cages used to manage freight of over 30 million parcels annually, CouriersPlease has enhanced operational efficiency and significantly mitigated the risk of asset loss.
Investing in secure tracking technologies, like 0G technology, helps supply chain leaders have a better handle on where their assets are, so they can manage risks more proactively.
3. Invest in automation to reduce human error
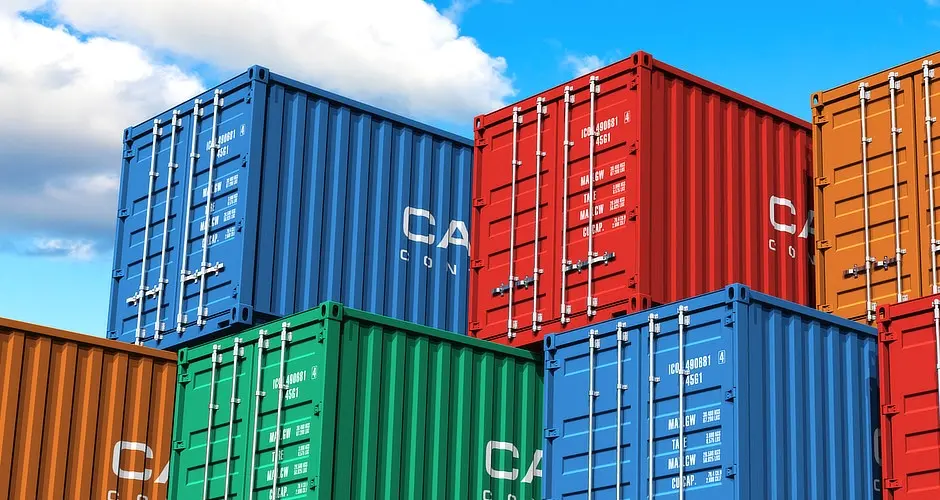
Tracking and tracing assets is the first step in improving supply chain visibility and lifting resilience. Still, an ERP system going down can compromise that data access. Therefore, relying on humans to gather data is not an efficient or resilient solution.
If you can get your assets to tell you where they are, there’s less reliance on systems and on your staff to manually gather data.
In the case of ASCAP, finding lost assets scattered across Australia took “a massive amount of work”. They were manually tracking them down, even physically putting employees on planes to fly interstate and retrieve returnable packaging units that had been lost in transit. This was before they deployed a successful IoT asset tracking project.
Within four months of ASCAP’s returnable packaging partner Loscam deploying an end-to-end IoT-enabled solution operating long range, long battery-life 0G-enabled devices, it discovered 5% of units were incorrectly delivered to a competitor’s warehouse and 8% of units moved outside the customer’s logistics provider network.
The technology brought a much-needed increase in visibility and control of assets, operational efficiency and asset utilisation. In one customer scenario, it reduced the number of units needed by 25%, enabling tens of thousands of dollars of savings to be passed onto customers each year.
Track, Trace and Tell technology also improves efficiency through automating manual tasks. If nobody has to scan packages anymore, because the package informs you of its location, human error is eliminated. There is less loss, less untraceable theft.
It’s all about enabling you to do less and get more accurate information faster.
4. Screen suppliers & document high-value data access flow
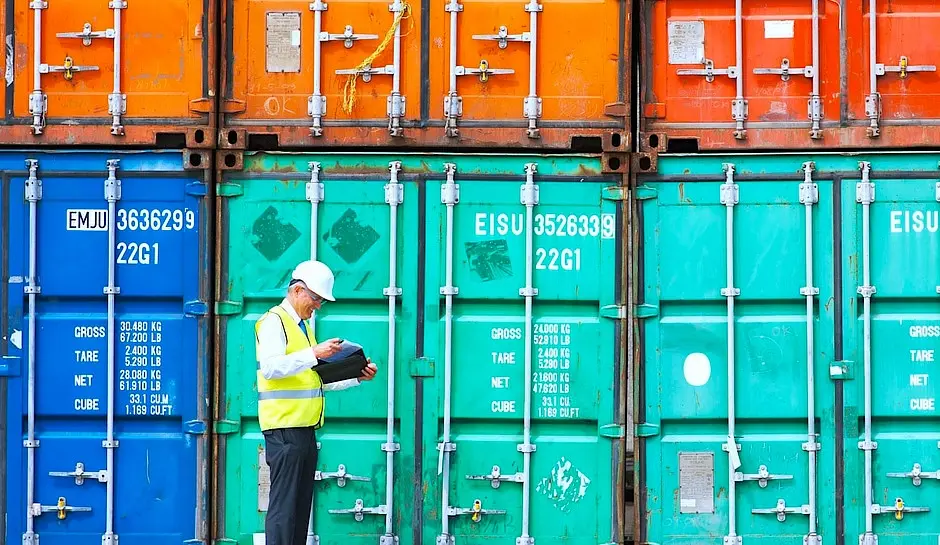
Supply chains are highly vulnerable due to the fact that they are, by nature, interconnected. Third-party suppliers can create something of ‘a weakest link’ if not inspected properly for their commitment to security.
Competitive supply chains need a flexible system of suppliers and partners that offer the ability to swap input materials and components and rapidly introduce new products.
Dun & Bradstreet researchers found that 51,000 companies worldwide, 163 of which are in the Fortune 1000, had one or more direct or “Tier 1” suppliers in Wuhan, China, the city where the coronavirus hit first, while at least 5 million — 938 in the Fortune 1000 — had one or more “tier 2″ suppliers there. The COVID-19 pandemic has highlighted the need for strong supply chain resilience, and it all starts with supply chain security.
There is no easy solution to ensuring end-to-end security, but organisations can start by defining their security requirements and thoroughly vetting each supplier before bringing them onboard as a regular partner. A recent Gartner report on supply chain cybersecurity also encouraged supply chain leaders to research and document the flow of high-value supply chain data and information across systems outside core IT systems.
Ensuring regular communication and a strong cyber-risk management program can help companies gain a deeper understanding of suppliers and enable stronger collaboration.
A multifaceted supply chain security strategy will cost money, but investing in strong risk management could save your company and your business.
Those who use a crisis to make investments and accelerate change come out better off. Resilient supply chains not only recover from disruption, but with the right level of investment, they can become a source of competitive advantage.
5. Embrace IoT technology
The Internet of Things (IoT) is transforming the supply chain management industry, enabling businesses to track goods from the point of manufacture to the point of consumption. By embracing IoT technology, businesses can collect data on their supply chains, which can help them identify potential issues before they escalate.
For example, IoT sensors can track the temperature and humidity of perishable goods during transportation, ensuring that they are delivered in optimal condition. A notable application of this is Konvoy’s innovative use of IoT to monitor the condition of kegs in their supply chain.
Konvoy has successfully implemented IoT sensors that provide data on the temperature and location of each keg, significantly improving the management of their assets and ensuring that craft beers are transported under ideal conditions.
IoT technology also allows for predictive maintenance. With IoT sensors placed on equipment and machinery, companies can monitor the health of their machinery, ensuring that it is always operating optimally.
Predictive maintenance can help companies identify potential issues before they cause any problems, reducing the risk of supply chain disruptions due to equipment failure.
6. Diversify your suppliers
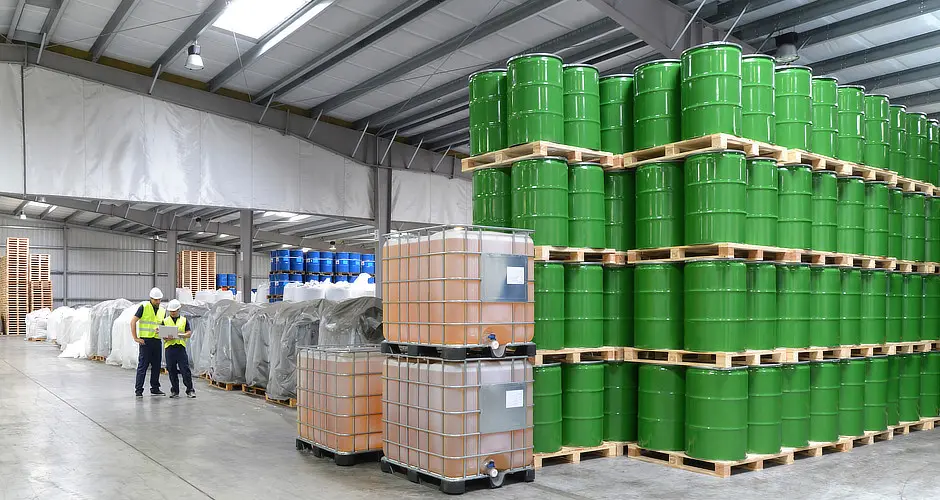
Relying on a single supplier can be risky, particularly if that supplier is based in a region prone to natural disasters or political instability. Diversifying your suppliers can help reduce the risk of disruption to your supply chain.
By working with multiple suppliers, businesses can spread their risk, ensuring that they can continue to deliver products or services even if one supplier experiences an issue.
In addition to reducing risk, diversifying your suppliers can also lead to cost savings. By working with multiple suppliers, businesses can negotiate better prices and terms, leading to more favourable contracts.
7. Develop a risk management plan
A risk management plan is a crucial tool for businesses looking to reduce risk in supply chain management. This plan should identify potential risks, such as natural disasters, supplier bankruptcies, or geopolitical risks, and outline strategies for mitigating those risks. The plan should also include a contingency plan that outlines what steps the business will take if a risk eventuates.
When developing a risk management plan, it is important to involve all stakeholders in the process. This includes suppliers, customers and employees.
By involving all stakeholders, businesses can gain valuable insights into potential risks and develop more effective risk management strategies.
8. Use data analytics
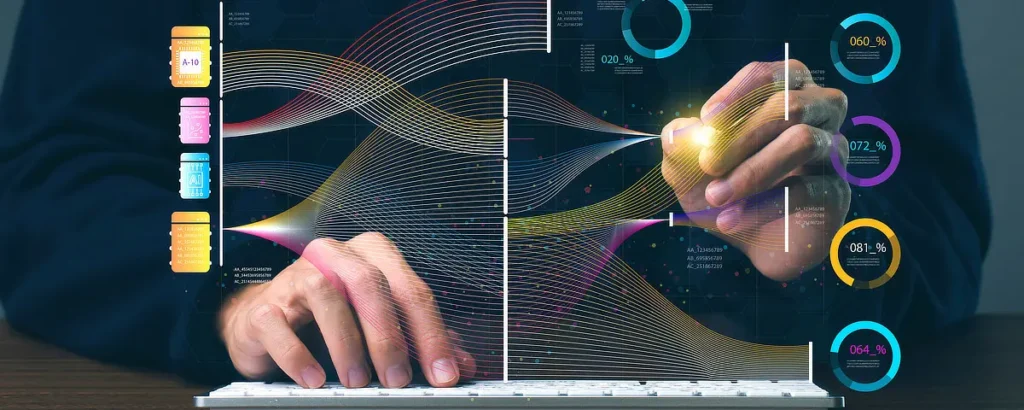
Data analytics can provide businesses with valuable insights into their supply chain operations. By analysing data on supplier performance, inventory levels and delivery times, businesses can identify potential risks and take steps to mitigate them. For example, if data analytics identifies a supplier that consistently delivers late, the business can take steps to find a new supplier to reduce the risk of supply chain disruption.
In addition to identifying potential risks, data analytics can also help businesses optimise their supply chain operations.
An example of the application of data analytics in optimising supply chain operations is Architectural Glass Products (AGP). Utilising IoT solutions, AGP has implemented data analytics to maintain their industry-leading, four-day order-to-delivery commitment.
The IoT-enabled tracking of over 1,750 delivery trolleys ensures that AGP maintains visibility over its assets, thereby facilitating the rapid and predictable delivery of high-value, fragile glass products. The data collected from IoT devices, provides AGP with insights into the location and status of these assets, significantly enhancing their operational efficiency and customer service.
9. Build resilience into your supply chain
Building resilience into your supply chain is key to reducing risk. This involves ensuring that your supply chain can adapt to changing circumstances, such as changes in customer demand or supply chain disruptions.
Businesses can build resilience into their supply chains by implementing flexible production processes, developing multiple distribution channels, and ensuring that their suppliers have contingency plans in place.
Implementing flexible production processes can help businesses respond quickly to changes in demand. For example, if demand for a particular product increases, a flexible production process can quickly ramp up production to meet that demand. This can help reduce the risk of stock outs and lost sales.
Developing multiple distribution channels can also help reduce risk. By working with multiple carriers and logistics providers, businesses can ensure that they have backup options in case one carrier experiences an issue. This can help reduce the risk of supply chain disruption due to transportation issues.
Ensuring that suppliers have contingency plans in place can also help build resilience into your supply chain. For example, if a supplier experiences an issue, a contingency plan can outline what steps the supplier will take to minimise the impact on your supply chain. This can help mitigate the risk of supply chain disruption due to supplier issues.
Don’t predict, plan
Supply chain organisations need to focus on what they can control, rather than what they can’t predict. By implementing these strategies, organisations can mitigate risks, improve supply chain visibility and reduce human error, resulting in more agile and resilient supply chain systems.
By embracing IoT technology, diversifying suppliers, developing a risk management plan, using data analytics and building resilience into their supply chains, businesses can reduce the risk of supply chain disruption and ensure that they can continue to meet customer demand even in challenging circumstances.